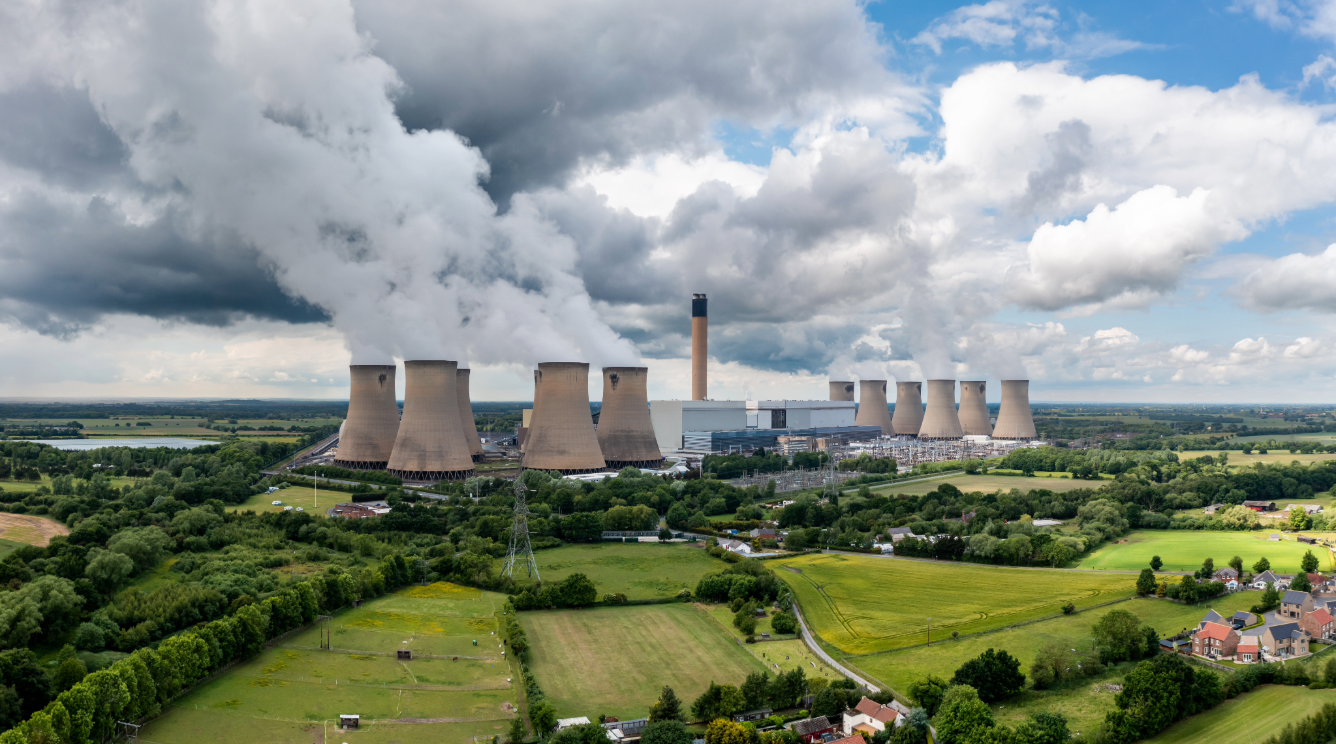
Technology aimed at separating and capturing carbon dioxide from industrial waste gases has been developed by the University of Sheffield in partnership with the Rotherham-based seal manufacturer AESSEAL.
The technology, called FluRefin, is currently being tested at the British Steel plant in Scunthorpe, where it is being used to capture carbon emissions from a boiler flue. The captured CO2 will be bottled in gas cylinders and taken back to the University of Sheffield to be converted into synthetic transport fuels.
FluRefin does not require the use of heat or hazardous chemicals and is much smaller and cheaper than other carbon capture technologies. It uses a pressure swing adsorption process – a technique used to separate mixtures of gases. This produces purified and importantly, anhydrous (dry) carbon dioxide as the product.
Dr Andy Trowsdale, British Steel’s Head of Research and Development, said that the initial aim was to test the extent of its capabilities.
“If it works,” Dr Trowsdale said, “it could be scaled-up to play an important role in carbon capture, utilization and storage."
While electrification of the steelmaking process will reduce emissions of carbon dioxide by more than 75 per cent, British Steel is looking to provide further reductions in CO2e (CO2 equivalent) intensity. This includes the development of technologies for capturing CO2 generated in other areas of its manufacturing operations.