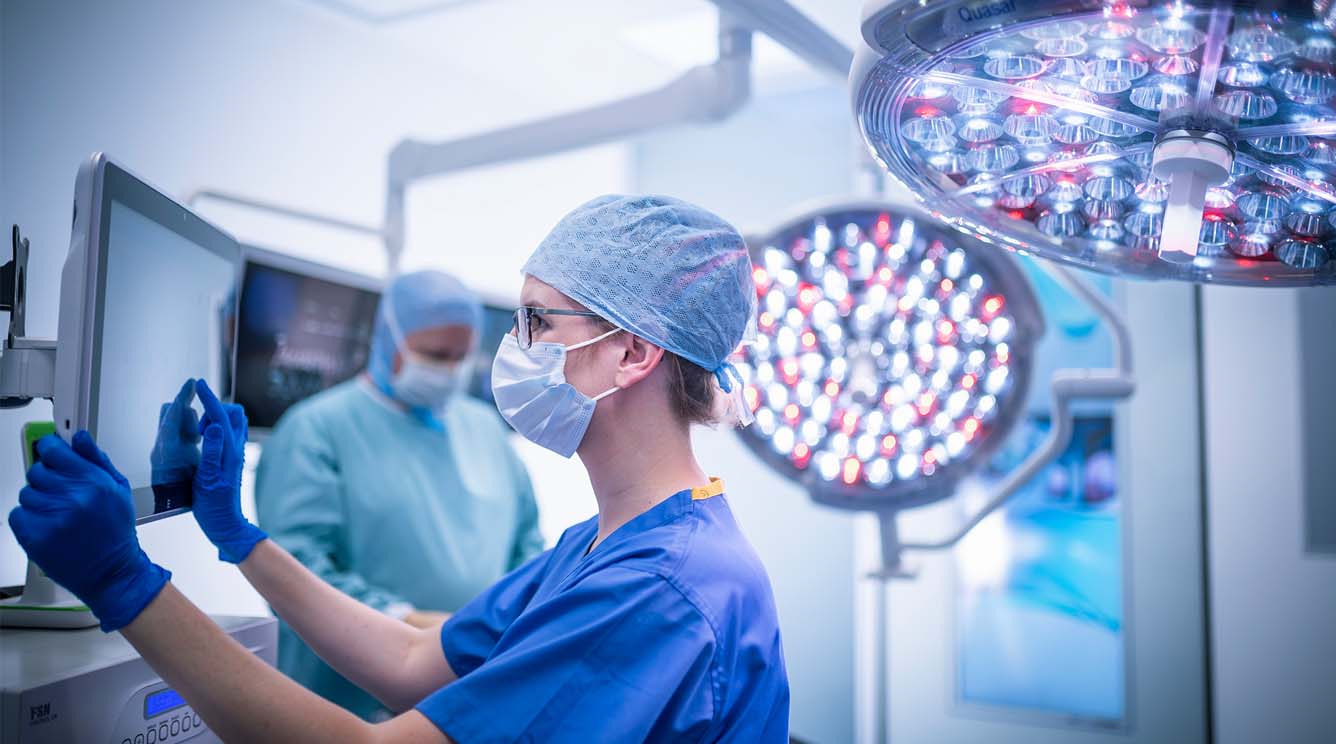
Brandon Medical is a relatively small company with around 75 employees, supplying specialist equipment for hospital operating theatres including lighting, medical video and controls.
We think that SMEs need to be part of the Net Zero solution, but many do not know where to start. There are so many reports, and so much advice about Net Zero, but not much tangible help.
Our recent journey has included controlling both our waste streams and energy use.
We have always tried to minimise what goes into general waste so we recycle aluminium and steel waste, cardboard, waste oils, cardboard, polyethylene and paper. In the beginning it was about cost and efficiency, now it is part of our philosophy of being a sustainable business.
Like many SMEs we did not have the luxury of building something perfect from scratch. When Brandon Medical needed to expand we bought an end-of-life building constructed to 1970s standards because it was 2.5 times bigger.
This older building was energy hungry with gas used for heating the factory, offices and providing hot water. It also used a lot of electricity. The old building had an Energy Performance Certificate (EPC) rating of F. We increased this to D when we moved into the building and have since upgraded this to a B-rating in 2021, which is about as good as can be achieved in a refurbished building.
Improvements were made by installing insulation and double-glazing, roof lighting, high efficiency heaters, ventilation, lighting, and advanced sensors and controls. We also invested in on-site generation from roof-mounted solar PV panels, as well as electric vehicles and charging points.
About 20-25% of our electricity is generated by solar energy. We currently have four fully-electric vehicles and two plug-in hybrid vehicles. The vehicles perform well but electric is still not a viable option for our delivery vans because of limited battery range. This is an area in which the available technology needs to catch up.
It is important to emphasise that the changes to our building have made them a more pleasant environment in which to work. We provide the right amount and type of light, heating and ventilation in the right place. For lighting, we use T5 and LED luminaires and employ daylight harvesting to maximise the use of sunlight.
We also have a Building Management System (BMS) with external and internal multipoint temperature sensors, rain sensors (to close sky lights), daylight sensors, light level sensors and presence/absence detection.
Our approach to Net Zero is as follows:
- We decided we want to do it!
- It is a journey not one project
- We started the journey with things we can do something about.
We decided to concentrate on Scope 1 and Scope 2 emissions: For us, Scope 1 means gas, petrol/diesel for our vehicles. Scope 2 is our external electricity supply.
We have been collecting and reporting our scope 1 and scope 2 carbon emissions for more than two years now.
It was interesting to discover that electricity (scope 2) is the biggest financial cost however gas (scope 1) is the biggest carbon emission. We could reduce our emissions simply by switching to a green electricity provider but we think we can do much more for the planet by reducing our energy use and by generating our own zero carbon energy. There is a logic to reducing electricity use first as it is a good thing to do and it is also the most economically viable.
Looking forward, our next plans are to investigate the use of an intelligent micro grid consisting of:
- Mains conditioning
- Power factor correction
- A second and bigger, solar PV array
- On-site battery storage
- A power management system to monitor sources and loads and to intelligently match them
- The provision of employee EV chargers for their private cars
As already mentioned, this is a journey and one of our priorities is to ensure that our staff are both engaged and pro-active. We have a volunteer employee sustainability team who are helping identify ways in which all staff can be involved and to think about scope 3 emissions in our supply and value chain.
The work streams under way cover:
- Document waste and recycling
- Mapping employee miles (to design a travel and work from home plan)
- Improvements to building insulation
- Turn-off policy (mainly computers, office equipment etc)
- Manufacturing process energy savings
- Improving our grounds for wild animals, carbon capture, our employees and visitors (Bee keeping, fruit trees, wild areas, recreational spaces)
Our company philosophy draws upon the Japanese ‘Kaizen’ approach which means concentrating on processes that continuously improve operations and involve all employees. It is a gradual and methodical process, systematically chipping away at things that can be improved.
When it comes to the Net Zero journey, if every SME finds 4,000 small things to change, it will make a huge difference.