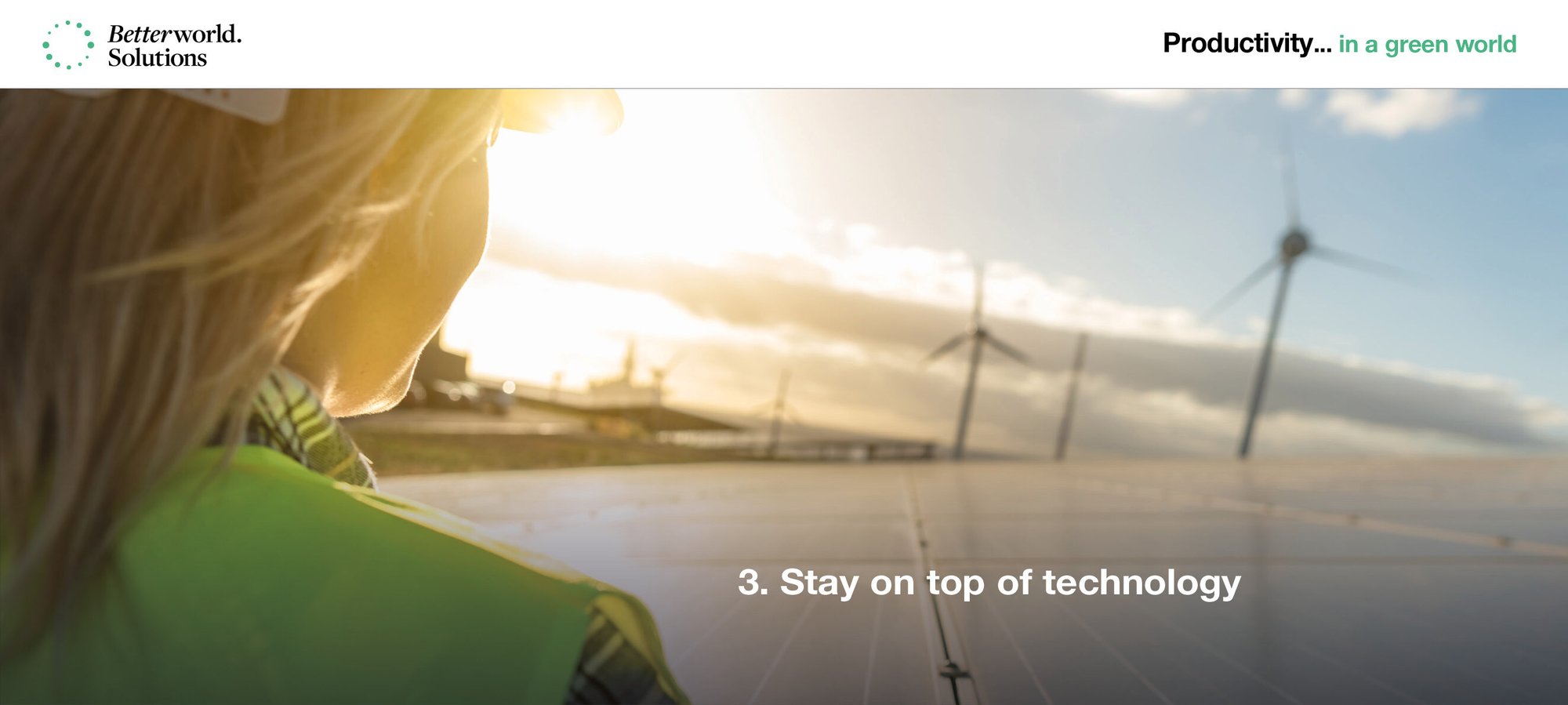
Stay on Top of Technology
Article 3 of 5 in the Productivity in a green world series
by Chris Rea
Managing Director of AES Engineering Ltd group
We live in a world that is increasingly digital, and this poses significant challenges for manufacturing organizations that have their origins in the material sphere.
There is no doubt about the continued importance of people in a successful and sustainable business, but ways of doing things are changing rapidly and whole job sectors are disappearing, meaning that skillsets need to be constantly refreshed.
This is the third article in a short series commissioned by the knowledge-sharing project Betterworld Solutions, to look at how traditional manufacturing companies, and indeed many other organizations, can be both green and productive – things that are key to long-term business survival.
This series is about productivity and sustainability, and it is a hard truth that businesses that want to survive need to be lean.
DCVIL stands for Designed, Configurable, Vertically Integrated Lean.
In previous articles I looked at how to Define a Customer (insert link) and at the importance of growing your own talent in Train to Win (insert link). Now I want to look at how technology has the potential to both destroy and create jobs, requiring managers, staff, and even customers to be both open-minded and adventurous.
A business that assembles to order is much more productive than any business that manufactures to order, but such a business needs to be designed right from the beginning, and having the right tools or technology is critical.
Manufacturing companies are often pictured in terms of buildings and machinery. In the case of AESSEAL® , in 2024 we doubled the size of our factory and completely re-imagined the space in order to create a Factory of the Future.
It is a showcase for sustainable business, with investment in robots, AI, and advanced end-to-end ordering and fulfilment. Cloud-based monitoring of customers’ machine tools delivers round-the-clock surveillance, and timely intervention.
This involved a massive investment in machine tools with a price range of £0.5 million to £1.75 million, plus a £2 million investment in AutoStore robots which double the efficiency of the picking part of the assembly operation.
Six CNC machine tool cells are on order. These are essentially robots as it is difficult or impossible to hire people to work 24/7, nightshifts, and in particular weekends and weekend nightshifts.
To remain productive in a high wage economy, we need to operate around the clock and throughout the year. Only robotically controlled machines will do that. However, there also need to be people in attendance – people with the right skills.
The skillsets required throughout the business are continually evolving and both hardware and software are driving change. Our digital roadmap includes automated quotations that give a customer certainty about when a vital order will be fulfilled.
With other tools, including our Design Automated Software, we are reaching towards a gold standard where more products and their common adaptations will not require time-consuming human design.
The first steps to embracing artificial intelligence are under way with the development of Brighty, the world’s first artificially intelligent mechanical seal expert – currently on internal testing. We are also developing Tosh – the world’s first artificially intelligent condition monitoring expert. The role of Tosh is to be able to predict when bearings are likely to fail.
The purpose of productivity enhancements is to serve our internal and external customers better. We do this by removing every repetitive, dull, boring, and unnecessary human intervention. This may do away with some existing jobs, but it can also create new career opportunities.
For the record, since 2020, AESSEAL® labour productivity has risen by 28%. During 2021-23 AES Engineering group sales from UK exports rose by 42%, increasing our employment in the UK by 13% to 790 and group employment to 2,010. In parallel, we invested heavily in the environment.
We need to get excited about change and grasp the opportunities – including the opportunities that lower our carbon footprints. Companies that don’t ride the technology wave are in danger of going under – and that doesn’t sound like fun.
In short, making your operation more productive and investing in your people and technology, creates long term sustainable jobs.
Note: This is the third in a series of four bite-sized articles commissioned by the Betterworld Solutions project to share information on sustainable business practices, with a special emphasis on encouraging global industry to prioritize investments that favour the environment. The first article was “Define a Customer” and the second “Train to Win”.
Don’t miss the final article in the series:
Get Emotional
AES Engineering is a global group headquartered in Rotherham in the United Kingdom that makes and sells high performance mechanical seals and provides reliability services to industry worldwide.
Our main global brands are AESSEAL® and AVT Reliability. We serve industrial sectors ranging from food and beverage to mining, oil and gas, pulp and paper, chemicals, and everything in between. Our highly engineered seals help the pumps and rotating equipment at the heart of almost all industries to work more cleanly and productively, with less harm to the environment.
Check out Betterworld Solutions, or follow my LinkedIn channel