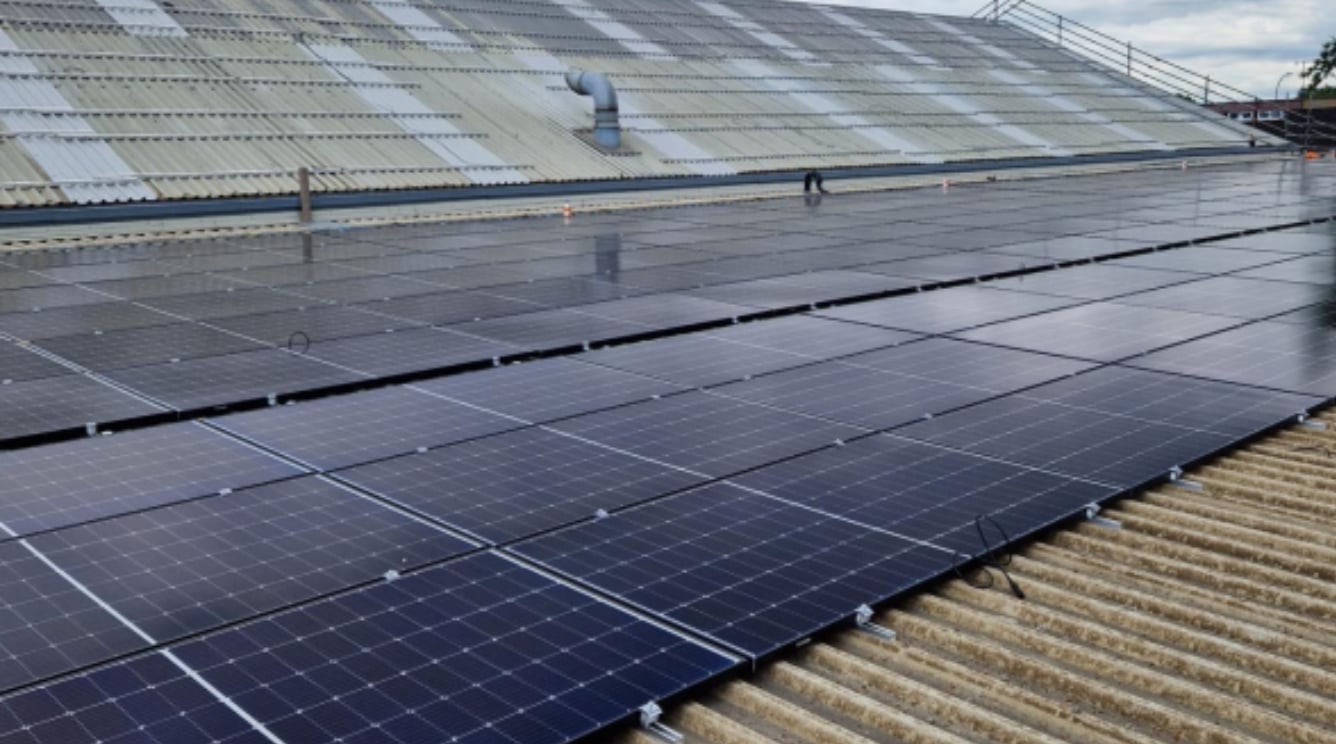
At OSL, intertwining our ambitious growth strategy with a rigid commitment to environmental responsibility has become a focal point of our wider corporate strategy. This dual commitment to excellence in both business performance and sustainable practice has seen a number of new initiatives launched across our Group; one such initiative was the introduction of Betterworld Water taps.
A water chilling and filtration device fitted under sinks across the Group, the Betterworld taps eliminate the use of plastic water bottle chillers and provide convenient access to cool drinking water without the use of excess plastic and the related detrimental environmental impact.
In total, we’ve installed seven taps throughout the Group, replacing 15 water bottle chillers. At a cost of £700 per chiller (£10,500 annually), compared with the cost of installing the Betterworld taps (£700), this amounts to a reduced expenditure of £5,600 annually. This represents a simultaneous financial and environmental benefit.
Alongside this, we’ve introduced reusable bottles across our businesses to encourage a reduction in single-use plastics. These initiatives are strongly aligned with our Group-wide ethos of individual efforts and accountability in our professional and environmental efforts. With approximately 300 staff members using our taps, these individual efforts combine to achieve a significant reduction in our carbon footprint as a collective.
Our Betterworld taps represent a strong commitment to the environment around us, incorporating sustainable practices into every level of our business and aligning new investments with our wider organizational objectives.
As well as this initiative, we’ve installed solar panels at our Burgess Road manufacturing site at a cost of £350,000, paying off the investment in 2-3 years with a projected first year carbon emissions saving of 53,444kg. This was accompanied by a £1.2 million investment in four new CNC turning lathes, allowing the retirement of several 25-year-old inefficient and outdated machines, and reducing energy use by 20-30%.
To consolidate the manufacturing operations of OSLCT, we also transported all of our manufacturing equipment from our second Sheffield site to Burgess Road, at a cost of £200,000. This is estimated to eliminate 10,000 miles of traffic between sites annually, as well as reducing our gas and electricity expenditures.
These investments illustrate a concerted passion for protecting our environment across our business portfolio. They demonstrate a shared understanding of the importance of sustainable business practices across our Senior Management Team, leading to the inclusion of positive initiatives throughout our strategic planning. By combining shrewd financial planning with a shared understanding of the importance of sustainable behaviors, we’ve worked to benefit both our business and the environment around us, further embodying our Group ethos; Entrepreneurship, Empowerment, and Excellence.