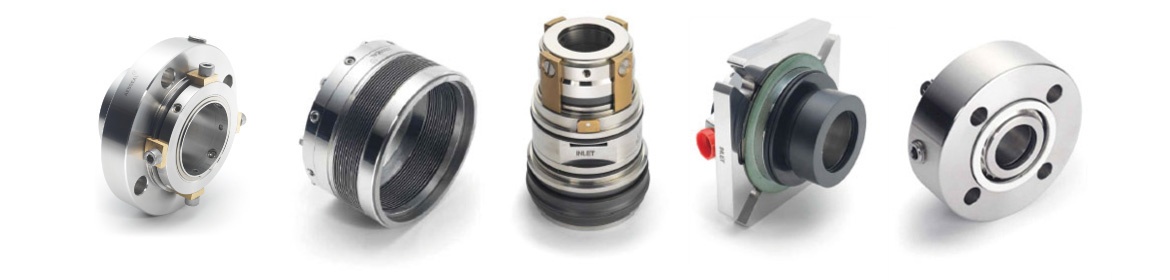
The savings can be achieved using existing energy saving technology some of which has been known for and been in use in a very small number of applications, but for more than 30 years.
The objective of this study is to estimate the potential energy savings which could be achieved through improving the efficiency of mechanical seal solutions utilised on plants around the globe.
This energy saving is expressed as a total of the number equivalent to an average car's annual CO2 emissions.
A global calculation is done for each industry considered, estimating the number of pieces of rotating equipment on an individual site/plant, then the number of specific sealing applications, the total utilisation of those pieces of equipment, expressed in hours and the total number of plants globally.
The model consists of the following calculations subject to the nature of the application studied and the available researched equivalent CO2 conversion factors for the fluids considered.
- Calculation of steam turbine steam loss savings achievable via installation of Gas Lift Mechanical Sealing technology - assuming 90kg steam Loss per hour.
- Calculation of the potential energy savings made by changing the sealing arrangement / API plan from least efficient to most efficient options, by way of reducing the need to heat up cool fluid injection from a continually fed external source.
Total (Approx) 341 million cars CO2 eq
*Mechanical Packing is used in all industries. In some regions or countries it is almost never used, yet in another region or country in the same industry it is in widespread use.
Calculation Assumptions
The calculations assume that all sectors are equally representative of the working assumptions and the model does not adjust for individual rotating equipment sectors which must vary and will be adjusted through verified feedback. It is recognised that some of these assumptions may not be correct and would welcome input so that we can further refine the model.
When calculating the energy required to replace the heat lost through cooling and the energy consumption, the following assumptions apply:
- No convection to atmosphere
- Cooler efficiency is 100%
- No viscous heat generation or losses
- No parasitic friction losses
- No throttle bushing leakage (plan 23)
- No circulating pump power loss (plan 54)
- No pressurising of flush or cooling water energy requirements considered
- Driver power not considered
Improved technology sealing systems available today can reduce significantly, or eliminate completely the need for energy-wasting systems that result in cooling/dilution of the process and the need for downstream separation/evaporation, re-heating, and/or effluent treatment.
Data available relating to high temperature pumps shows frequent use of energy-wasting seal support systems.
This study focuses exclusively on applications above 200°C. Based on previous studies by the FSA and ESA of 28,000 seal applications, 18% of these represent applications where pumping temperatures exceed 200°C were using API Plan 32, as well as 7.5% using API plan 21(see 'Energy Savings Opportunities Application of energy saving sealing technologies to replace current industry practice, FSA & ESA, Feb 2011)
Using this information for the sake of the calculations, 20% and 10% have been used as rounded proportion figures for API Plan 32 and API Plan 23 respectively.
These proportions have been applied to all the industries studied. The authors accept these may not be specifically representative for the industries studied when looked at on an individual basis and we welcome feedback to help further refine the calculations. However when looking at the global totals it is expected this balances out across all industries when these are considered as a whole.
It is expected more savings can be made elsewhere, however this study does not consider the remaining 70% of applications which may be lower than 200°C. At the lower temperatures contributions to savings are expected to be significantly less and therefore were not considered. Our conservative estimate is that this may be accounted for by adding 20 to 30% on top of the final total energy savings determined by this study.
For Calculation B1 the power consumption for plan 32 is taken as 162kW. This is taken as an average between the two least efficient plan 32 applications (Case 2A and 2B given in the FSA and SA 2011).
For Calculation B2 the power consumption for plan 21 is taken as 40kW (FSA and ESA 2011).
A significant initiative will be needed to educate industry on the potential for energy savings through the adoption of improved sealing system designs.
If you would like to help further improve the model and have some data to refine our assumption please contact us